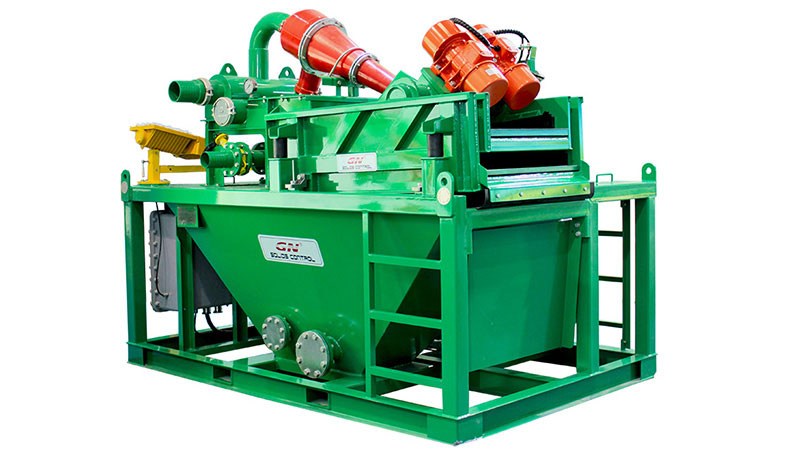
The GN Piling Mud Desander Plant is a scientifically designed and technologically advanced system for the effective treatment and recycling of piling mud. It is widely utilized in various applications, including Bored Pile Slurry desanding plants, TBM (Tunnel Boring Machine) slurry treatment, HDD (Horizontal Directional Drilling), and water well drilling, among others.
Model | GNMS-200D | GNMS-500D | GNMS-100D |
---|---|---|---|
Capacity | 50m3/h(200GPM) | 120m3/h(500GPM) | 240m3/h(1000GPM) |
Cut Point | 25 microns | 40 microns | 40 microns |
Mud Cleaner | GNZY753E-Y4NF | GNZY753E-Y1S | GNZY705E-Y2S |
G Force | ≤7.1G(adjustable) | ≤7.1G(adjustable) | ≤7.3G(adjustable) |
Bottom Screen Area | 1.35㎡ | 1.35㎡ | 2.6㎡ |
Upper Screen Are | 0,875㎡ | 0,875㎡ | 1.35㎡ |
Cyclone Size | 4inch | 10inch | 10inch |
Cyclone Qty. | 4pcs | 1pc | 2pcs |
Cyclone Feeding Pump | GNSB4x3C(11kw) | GNSB5x4C(30kw) | GNSB6x5C(45kw) |
Total Power | 13.11kw | 32.11kw | 48.99kw |
Inland Shipping Size (mm) | L3134xW1920xH2521 | L3135xW1920xH2431 | L3720xW2170xH2528 |
Operation Size (mm) | L3506xW2060XH3786 | L3506xW2060XH3786 | L4176xW2215XH3759 |
Total Weight | 3012kg | 3377kg | 3733kg |
The piling mud is drawn from the mud pit by a slurry pump and directed to the bottom layer screen of the shale shaker (3) through a buffer box (2). Within this process, coarse particles are effectively separated, and the remaining mud is then directed to the mud storage tank (4) via the bottom layer screen. Subsequently, a centrifugal pump (5) draws mud from the recycling tank (4) and delivers it to the desander cone (6) under pressure, enabling efficient centrifugal separation of solids and sand. The discharged solids and sand are directed to the upper shaker (3) through the outlet nipple of the desander cone. After undergoing the dewatering process on the upper shaker (3), the fine solids are effectively separated. The clean mud is then returned to the recycling tank (4) through the upper shaker screen, while the remaining mud enters the intermediary tank (7) via the desander cone overflow pipe. Depending on the fluid level in the recycling tank, the mud in the intermediary tank (7) can be discharged through the outlet pipe (9) or redirected back to the recycling tank (4).
To maintain balanced fluid levels within the system, a fluid level float switch (8) is positioned between the intermediary tank (7) and the recycling tank (4). When the mud level in the recycling tank (4) is low, the overflow from the desander enters the recycling tank (4) through the intermediary tank (7). Conversely, if the mud level in the recycling tank (4) becomes excessively high, the mud will overflow to the intermediary tank (7) and be discharged via the outlet pipe (9). For operators aiming to achieve high-quality clean fluids, reducing the feeding capacity to the system and implementing repeated cleaning processes can yield optimal results.
As a reputable manufacturer of shale shakers, desanders, desilters, and decanter centrifuges, GN Solids Control offers complete and tailored solutions for Piling mud or slurry treatment projects. Each equipment serving a specific purpose in the solids separation process.
The shale shaker is responsible for efficiently separating coarse solids, while the desander excels in the separation of sands. For the removal of silts, the desilter is employed, and the mechanical centrifuge effectively separates fine solids. To tackle the challenge of ultra-fine solids, GN Solids Control utilizes chemically enhanced technology combined with a decanter centrifuge, resulting in the efficient separation of these minute particles and facilitating the discharge of clean water.