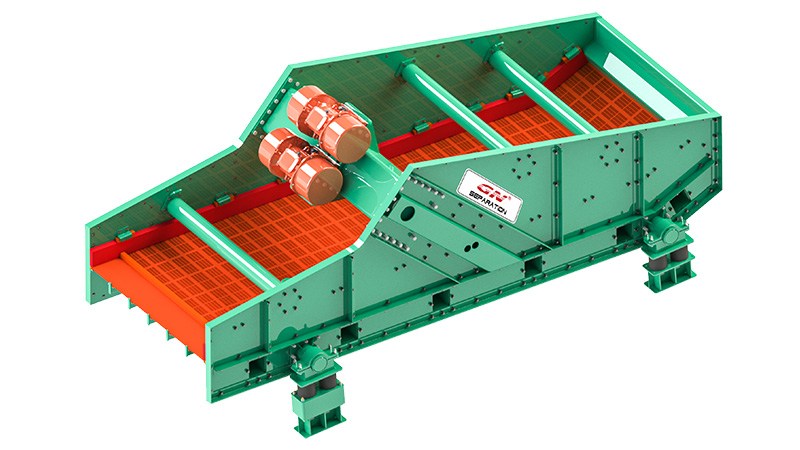
The GN Dewatering Vibrating Screen finds extensive applications across various industries, including mining, coal, construction materials, metallurgy, and chemicals. This high-performance vibrating screen employs linear motion and is particularly effective for dewatering, desliming, demineralization, and dry discharge of mining tailings. Its versatile design and efficient functionality make it an indispensable asset in several industrial processes.
The GN Dewatering Vibrating Screen is extensively employed in the mining, coal, construction material, metallurgy, and chemical industries. Its linear motion design makes it perfect for dewatering, desliming, demineralization, and dry discharge of mining tailings. Incorporating advanced features like finite element analysis and anti-fatigue analysis, the screen boasts a well-structured design with low energy consumption, high dewatering capacity, and efficient dry discharge capabilities. Its adaptability to corrosive and abrasive working conditions enhances its reliability across various environments.
This equipment is equipped with two vibrating motors, utilizing the principle of reverse self-synchronization to drive linear movement of the screen body. The resulting synchronous vibration of the screen surface exerts force on the materials, facilitating solid-liquid separation and sorting particles by size. The continuous feeding of materials directly from the feed tank or cyclone ensures smooth dewatering and disintermediation on the screen surface. The separated materials above and below the screen are efficiently discharged into the upper and lower receiving tanks, respectively, for further processing in subsequent stages.
To cater to diverse material properties at customer sites, the included angle between the vibration force direction and the horizontal axis can be customized. This angle directly influences the material's speed on the screen surface, ultimately optimizing the equipment's processing capacity. With its remarkable processing capacity, high efficiency, and stable performance, the GN Dewatering Vibrating Screen stands out as a versatile and customizable solution suitable for various industrial applications.
Model | GNLMZ1236 | GNLMZ1536 | GNLMZ1836 | GNLMZ1848 | GNLMZ2448 |
---|---|---|---|---|---|
Screen Area | 4.32 m2 | 5.4 m2 | 6.48 m2 | 8.64 m2 | 11.52 m2 |
Vibration Direction Angle | 38~52 Degree | ||||
Vibration Frequency | 16 Hz | ||||
Power | 2*2.9 kW | 2*2.9 kW | 2*4.5 kW | 2*5 kW | 2*7 kW |
Double Amplitude | 4~6 mm | ||||
Screen Opening | 0.2-25mm | ||||
Dry Material Discharge Capacity | 8~20 m3/h | 12~25 m3/h | 24~32 m3/h | 25~35 m3/h | 30~45 m3/h |
Installation Inclination ° | ±4 | ||||
Remark |
|
||||
The above specification and parameters for reference only. |